Cement concrete possesses the following important properties:
- It possesses a high compressive strength.
- It is free from corrosion and there is no appreciable effect of atmospheric agents on it.
- It gives a hard surface capable of resisting abrasion.
- It is more economical than steel, as sand and coarse aggregate, which constitutes the bulk of concrete, are generally available at a cheaper rate. Formwork can be reused for other construction works.
- Improved appearance and various types of finishes can be given to the concrete surface.
- It continues to harden and attains more strength as time passes. It is this property of cement concrete that gives it a distinct place among the building materials.
- It can develop good bondage with steel. Steel reinforcement is usually placed in cement concrete at suitable intervals to take up the tensile stresses, as plain concrete is weak in tension. This is termed as Reinforced Cement Concrete or RCC.
- Due to the presence of voids in the concrete, which are formed during its placing, it has a tendency to be porous. This can be checked by
- The use of minimum water–cement ratio
- The proper grading of aggregates and
- Better compaction after placing the concrete.
- Due to loss of moisture with time, the cement concrete has a tendency to shrink. The shrinkage can be reduced by proper curing of the concrete.
- The concrete mixes are designated as M10, M15, M20, M25, M30, M35 and M40. ‘M’ refers to the mix and the number denotes the ultimate strength of concrete mix in N/mm2 at the end of 28 days.
Strength
Concrete is to be strong enough to withstand the stresses caused on it with a required factor of safety. The strength of the concrete is measured in N/mm2 as said earlier and it is the ultimate compressive strength of 15 cm cubes after 28 days of curing (sometimes 7-day curing strength is also found out).
The tensile strength of concrete is about 8–12 per cent and shear strength is 8–10 per cent of its compressive strength.
Durability
Concrete should be able to resist the forces of disintegration owing to natural and chemical causes. The durability of concrete can be increased by using good quality materials, adopting optimum water–cement ratio, using dense graded aggregates, careful mixing and placing through compaction and adequate curing.
Workability
Workability is the easiness with which the concrete mix can be mixed, handled, transported, placed, moulded and compacted. A workable concrete should not show any segregation or bleeding, i.e., the materials should not separate out or the excess water should not come up to the surface.
The workability of concrete can be measured by two tests, namely the slump test and the compacting factor test.
Slump test
The slump test is carried out to have a rough estimate of the workability of concrete. It does not measure all factors contributing to workability, nor is it always representative of the placeability of the concrete. However, it is conveniently used as a control test and gives an indication of the uniformity of the concrete from batch to batch.
The apparatus for conducting the slump test essentially consists of a metallic mould in the form of a frustum of a cone having internal dimensions as follows:
Bottom diameter | – | 20 cm |
Top diameter | – | 10 cm |
Height | – | 30 cm |
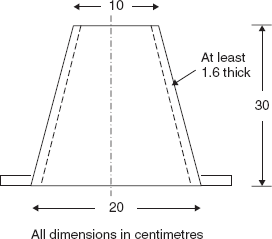
Figure 16.2 Typical mould for slump test
Figure 16.2 shows the details of the slump apparatus.
The internal surface of the mould is thoroughly cleaned and freed from any superfluous moisture. The mould is placed on a smooth, horizontal, rigid and non-absorbent surface. The mould is then filled in four layers, each approximately one-fourth of the height of the mould. For tamping the concrete, a steel tamping rod of 16 mm diameter and 0.6 m length with a bullet end is used. Each layer is tamped 25 times by the tamping rod. After the top layer has been rodded, the concrete is struck off level with a trowel and tamping rod. The mould is removed from the concrete immediately by raising it slowly and carefully in a vertical direction. This allows the concrete to subside. The difference between the height of the mould and that of the subsided concrete is measured in mm and this is referred to as the slump of concrete.
It is seen that the slump test gives good consistent results for a plastic mix. This test is not sensitive for a stiff mix. Despite many limitations, the slump test is very useful on site to check the day-to-day or hour-to-hour variation in the quality of the mix.
Slumps for different works
The recommended slump for concrete for different types of works is shown in the table.
Number | Type of concrete | Slump |
---|---|---|
1 | Concrete for road construction | 20–40 mm |
2 | Concrete for top of curbs, parapets, piers, slabs and walls that are horizontal | 40–50 mm |
3 | Concrete for canal linings | 70–80 mm |
4 | Concrete for arch and side walls of tunnels | 90–100 mm |
5 | Normal RCC work | 80–150 mm |
6 | Mass concrete | 25–50 mm |
7 | Concrete to be vibrated | 10–25 mm |
Factors affecting workability of concrete
The major factors affecting the workability of concrete are given below:
- Water content
- Mix proportions
- Size of aggregates
- Shape of aggregates
- Grading of aggregates
- Use of admixtures
- Water content: Water content in a given volume of concrete will have a significant influence on the workability. The higher the water content per cubic metre of concrete, the higher will be the fluidity of concrete, which is one of the important factors affecting workability. However, increasing the water content must be the last option to be taken for improving the workability. More water can be added, provided a correspondingly higher quantity of cement is also added to keep the water–cement ratio constant, so that the strength remains the same.
- Mix proportions: Aggregate–cement ratio is an important factor affecting workability. The higher the aggregate–cement ratio, the leaner is the concrete. In the case of lean mix, less quantity of paste is available for providing lubrication and, hence, the mobility of aggregate is restrained. On the other hand, in the case of rich concrete with lower aggregate–cement ratio, more paste is available to make the mix cohesive and fatty to give better workability.
- Size of aggregates: The bigger the size of aggregates, less quantity of water and paste will be required. Hence, for a given quantity of water and paste, bigger size of aggregates will give greater workability. The above will be true within certain limits.
- Shape of aggregates: The shape of aggregates greatly influences the workability. Angular, elongated or flaky aggregates make the aggregate very harsh when compared to round- or cubical-shaped aggregates. Contribution to greater workability of rounded aggregates is due to the fact that for a given volume or weight it will have less surface area and less voids than angular or flaky aggregates.
- Grading of aggregates: This is one of the factors which will have maximum influence on workability. A well-graded aggregate is the one which has least amount of voids in a given volume. Other factors being constant, when the total voids are less, excess paste should be available to give better lubricating effect.
- Use of admixtures: Of all the factors, which affect workability, the most important factor is the use of admixtures. Admixture is defined as a material, other than cement, water and aggregates, that is used as an ingredient of concrete and is added to the batch immediately before or during mixing. Plasticizers and superplasticizers are admixtures that greatly improve the workability many folds. The use of air entraining agents reduces the internal friction between the particles and gives easy mobility to the particles. Similarly, the fine glassy pozzolana materials, in spite of increasing the surface area, offer better lubricating effects for increasing the workability.
Leave a Reply